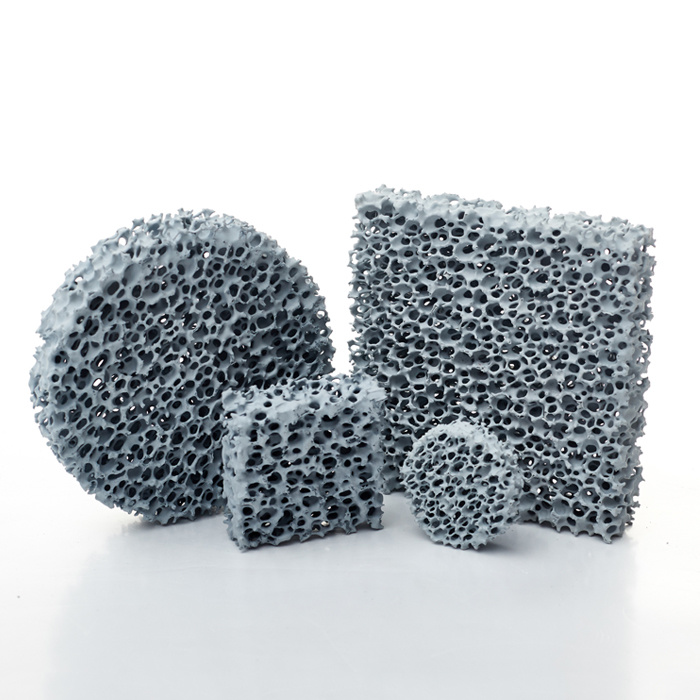
Yuantai silicon carbide foam ceramic filter is widely used in the casting process of ductile iron, gray iron, malleable cast iron and other cast iron. Its ultra-high temperature strength, compressive strength, micron filtration accuracy provides a favorable guarantee for the improvement of casting quality.
Foam ceramics is a kind of porous ceramics similar to foam in shape, which is the third generation of porous ceramics developed after ordinary porous ceramics and honeycomb porous ceramics.
This high-tech ceramic has three dimensional connected pores, while its shape, hole size, permeability, surface area and chemical properties can be moderately adjusted and changed, the product is like "tempered foam" or "porcelain sponge".
As a new type of inorganic non-metallic filter material, foam ceramic has the advantages of light weight, high strength, high temperature resistance, corrosion resistance, simple regeneration, long service life and good filtration absorption. Foam ceramic filter is generally filled with foam sponge with ceramic paste, and then extruded the paste, the remaining coated ceramic material around the foam fiber, sintering at high temperature, foam sponge heat decomposition, leaving foam ceramic products is foam ceramic filter, the filter according to different ceramic materials can be used for various casting alloys.
With its internal interconnecting three-dimensional structure, the foam ceramic filter can fully reflect its rectification, mechanical screening, "filter cake" and adsorption four filter mechanisms when filtering molten metal, while the filter material has good chemical stability, does not react with the alloy liquid, so as to effectively remove or reduce the inclusions in the metal liquid, to improve the purity of the metal liquid. The surface of the cast metal castings is smooth, the strength is improved, the scrap rate is reduced, and the machining loss is reduced, thereby reducing energy consumption, improving labor productivity and reducing costs.
Ningxin silicon carbide foam ceramic filter is used to improve the quality of ductile iron, gray iron, malleable cast iron and other castings, which can effectively remove non-metallic inclusions in metal melt and reduce the turbulence of metal melt. Product indicators meet the requirements of standard GB/T 25139-2010.。
Product features:
The grouting is sufficient and there is no blind hole, forming a multi-dimensional channel with complete hole reinforcement
Ceramic material enough, computer temperature control sintering, sintering temperature is high,
It has excellent thermal shock resistance, alloy erosion resistance and high temperature strength
Standard size, finished product through simulation booth testing to ensure consistency
The use of special binder and post-treatment process, no slag
Good porosity to ensure good flow of hot metal
Benefits of using filters:
Simplify the casting system and improve the casting yield
Effective removal of non-metallic impurities in hot metal
Reduce turbulence, maintain the consistency of hot metal flow, reduce the occurrence of bubbles
Improve the mechanical properties of castings, reduce machining wear and reduce costs
Comprehensive reduction of castings scrap rate
Application: Cast iron, cast copper, non-ferrous metal and its alloy casting.
* Can be customized according to customer requirements of different sizes and hole density products.
Shape: square, rectangle, circle.
Square size range: 35x35mm-360x360mm.
Round size range: diameter 40mm- diameter 360mm.
Thickness size range: 11mm-40mm.
The dimensional tolerance can be controlled within the upper and lower deviation of 2mm. Because the size of the base or slot where the filter is placed also has tolerances, the filter dimension tolerance needs to be confirmed by the user.
Selection of ceramic filter size and mesh:
Considering the cleanliness of the metal liquid and the pouring temperature, the flow control area is calculated to meet the requirements of the pouring time
Try to use an open casting system to avoid air trapping
Filter area is selected according to filtration capacity and casting time requirements
Silicon carbide foam ceramics filtration capacity (Kg/cm2) : gray iron :4.0 ductile iron :2.0 alloy cast iron :1.0-2.0
Mesh selection: general gray iron with 20ppi, ductile iron with 10ppi. 15 or 25ppi can also be selected, and the choice of mesh is related to many factors in the actual casting.
Filter location:
Placed in the pouring cup: more commonly used for precision casting and iron mold sand casting.
Placed at the bottom of the runner: It is often used for the case that the full box casting iron is not much, especially for the casting system where the straight runner is located in the center of the cast and has multiple cross runner branches.
Placed horizontally in the runner: the metal liquid filling is smooth, avoiding the direct impact of the metal liquid on the ceramic filter. The slag retaining function of the upper half runner is well played, and it is conveniently placed.
Vertically placed in the cross runner: the liquid metal flow rate is fast, has a good filling ability, the liquid metal directly impact the surface of the ceramic filter, should consider the impact resistance of the ceramic filter.
Ceramic filter base or card slot design: to fully consider the filter placement convenience (such as cone, slope, gap, etc.) and firm and reliable. The casting support surface at the place should be rounded (scrunching) to prevent the inflow surface of the sand flushing hot metal from leaving a support width of more than 5mm. The gap between 1-1.5mm and the sand collecting groove are